Traditional lumber companies are big volume businesses. They need to take the biggest trees as easily and quickly as possible. Many then ship the trees from the US to China to turn them into boards and ship them back. Each board has been transported thousands of miles multiple times. Ridiculous & very bad for the environment.
How is TreeHugger Tree Farm different?
First, we own the land we are working and - as you might guess - we care about it deeply. We want it to produce healthy trees and a wide variety of species. Over-harvesting one species is detrimental to the entire ecosystem.
Low Impact Harvesting
Instead of big destructive machines and trucks, we use low impact logging methods. We fell our trees with planning & precision. We carry trees out with an ATV and a fetching arch. Our intricate trail system allows us to tread on the forest floor as little as possible.
Worst First
We choose trees based on the worst-first doctrine. Basically, we take the dead, dying or less healthy trees before taking the bigger healthier ones. Why? We want the healthy ones to grow and produce for as long as possible. Remember...this is our land and our trees, so patience is not only virtuous but good business sense! By doing this, our forest gets healthier and more productive every year.
Locally produced
Our trees travel less than a half mile (sometimes just 100 ft) to our Woodmizer sawmill. The Woodmizer earns its name from minimizing waste while producing beautiful lumber.
Air & Sun Powered drying process
The wood is then air-dried in stacks covered by metal to protect from the rain. After a few weeks, the wood is about 15% moisture content and ready for our Solar Kiln we built in 1992.
Our solar kiln will further reduce the moisture content to between 6-8%. At this point the wood is stable and ready to be turned into flooring. In the picture to left, you can actually see the water from the wood condensed between 2 layers of plastic. The water drips out the bottom.
We then edge the wood & plane it close to finish size. The next step is our 4 sided planer molder. This machine cuts the tongue & groove while planing the top and bottom to the finished size.
Mixed Widths
We determine the best width for each board to maximize the yield and minimize the waste. Currently we produce 2 1/4in, 3 1/4in & 4 1/4in boards.
Scraps used as fuel
In addition, scraps are used in our outside water stoves to heat our homes & water.
Eco-minded floor sealers
When installing floors, we use the best waterbased sealers and finishes.
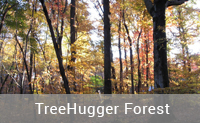
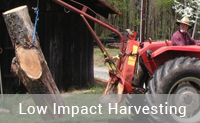
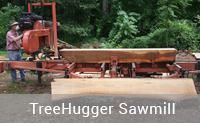
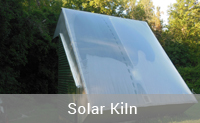
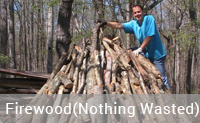